Will Electric Cars Drive Smart Tires?
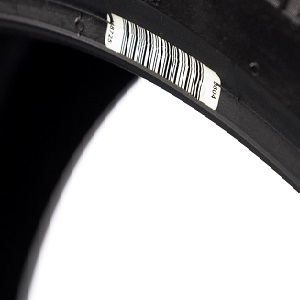
The world around us is rapidly transforming, thanks to data which is being extensively shared by end-users, value chain owners, and manufacturers. This type of data driven model will transform the relationship between drivers, OEMs and tire manufacturers, and if embraced by the industry, will provide capabilities to the OEM and tire industry to deliver safer and higher quality user experience.
Use cases developed around Smart Tires identify a number of benefits with the most important ones leading to an increase in safety and reliability, which are often tied to the tire manufacturer’s quality improvements and reduced liabilities.
With the rise of electric cars, the tire industry is under increasing pressure around the globe to deliver so-called “Smart Tires”. On one hand for ensuring safety and quality through the increased end-to-end traceability, on the other hand more and more parts are becoming “connected” to each vehicle for better integration and driver experience. Tires, although one of the most critical consumable components, seem to still be disconnected from the majority of vehicles on the market today.
Last month Tesla announced it was launching its new “Cheetah mode.” The world is already familiar with the Tesla “Ludicrous mode” which offers a mind-bending instant acceleration from standstill. The “Cheetah mode” goes a step further. When this mode is turned on, the vehicle’s dampers are lowered (such as a cheetah just before the attack) and the car sprints from 0-100km/h in 2.6 seconds. Previously, Tesla drivers were already waiting in anticipation for the traffic lights to turn green so they could have an opportunity to experience the 2.9 seconds acceleration of their Performance Model X as it sprints to the 100km/h. The 0.3 seconds improvement for the new Cheetah mode does not seem like much, but to put it into perspective, it translates to slightly more than a 10% improvement in acceleration. A quick search shows that there are only a few other standard production cars on the market that offer similar acceleration performance, and they include the likes of Porsche Taycan Turbo S, the Bugatti Chiron, 2020 BMW M8 Coupe Competition, or the Lamborghini Huracán EVO. The big difference, however, is that, whether or not we factor in subsidies for electric vehicles, a Tesla is becoming accessible to more drivers than exotic supercars. Exotic supercars are available in limited numbers, for eye-watering prices, and built from superlight exotic materials. Among many aspects, weight is a large contrast between fast and powerful exotic cars, and mass-produced electric vehicles. Some Tesla models weigh as much as 2.5 tons, where many high-performance cars, or even combustion engine cars, weigh far below that.
The tire industry designers struggle with balancing various important tire parameters such as rolling resistance, noise, wear, grip on dry and wet road surfaces, braking distance, etc. It is also very important to know in which climate and conditions a tire will be used. Electric cars, which look like our everyday passenger cars or SUVs, weigh 30% – 50% more than similarly performing vehicles but deliver limited-edition-exotic-supercar levels of torque and acceleration, require long lasting tires. This equation presents the tire industry with nearly impossible task. And we have not even factored in the different needs of drivers who want to use their Tesla like a Formula 1 car, compared to the drivers who purchase an electric car for environmental responsibility.
In the Tesla, “Cheetah mode” example, a regular everyday driver gets access to performance capabilities available only to professional race car drivers or the few high-performance exotic car drivers. It is highly questionable that all the drivers among us understand the direct impact a tire and its conditions have on the handling and safety of regular driving, let alone driving at much higher limits. This also begs the question if, for example, every Tesla driver, is able or willing to purchase the proper model and rating of very expensive OEM specified tires when they need replacing. At the same time, why should an environmentally conscious conservative driver purchase expensive, short life high-performance tires, when average all-season tires are perfectly suited to his or her driving style?
The conclusion is that there is a great need to be able to identify each tire both during the production process and during the use of the tire. Radio Frequency Identification (RFID) is the technology that makes it possible to automatically capture all data from the construction phase of the tire without additional operations or major investments. Drivers and OEM providers are empowered with all the data they need to make optimal decisions when selecting tires for their vehicle.
The trend within the automotive industry is more and more to create a connected car which are communicating with each other about e.g. road conditions and weather. In the future, the needs and profiles of the individual users of a car will be stored in the cloud. The moment all tire data is associated with the car, and driver behavior it is very easy to communicate with the driver in real time about the tires combined with speed, weather conditions etc.
One of the big challenges for the tire and automotive industries is who owns and who has access to the data available from cars, tires, and other connected devices. The moment the OEM shares this specific data, the tire producer will be able to produce faster and better tires in smaller batches specifically produced for a small group of users. In this case the driver using his Tesla as a F1 car will be able to buy the best tires for his use, and the driver whose primary concern is the environment can get tires optimized for completely different purpose to safely work on his Tesla.
But at the moment the tire industry is simply facing the challenge of how to integrate a “foreign device” such as an RFID transponder in a tire construction they have been working decades to perfect. And do this without impacting safety, quality, or cost. This is not a simple task for a traditionally conservative industry. The tire industry can approach this with two different mindsets. One, they let their customers, mainly the automotive industry, mandate RFID requirements. This has been the case across many other industries. It typically puts the manufacturer into a reactive position of following requirements and not having the opportunity to define its own benefits and business cases. The other approach is proactive, putting the manufacturer in an advanced position with understanding the technology, use cases, business cases, and benefits for internal and customer applications.
The proactive approach puts tire manufacturers in a position to address needs and problems within their own production facility and throughout the supply chain:
- Tracking and tracing of production process steps and the association of these processes to the individual tire;
- Association of the tools and materials used in the production of the individual tire;
- In-bound and out-bound logistics together with accurate inventory management across the tire supply chain;
- Association of tires to rims and vehicles, and the vehicle being able to identify specific tire to improve safety, performance, and user experience according to road and equipment conditions in real time (e.g. tire pressure, temperature, speed, acceleration, road condition, wear, compatibility, etc.);
- Collection of usage data. This input helps aggregate big data for predictive modeling to meet the individual needs of the driver;
This is how enabling Smart Tires with RFID works:
On the individual building machine there is a roll of RFID bead labels individually coded, printed and coupled to the batch of tires which are going to be produced by this specific machine. The RFID barcode bead label will be applied in the bead area or, on the inner liner of the green tire. From this point every process step can be automatically coupled to this individual tire such as molds, bladder and press. After vulcanization, the RFID barcode bead can still be read at around 4 to 5 meters by using a RFID handheld reader or portal. At quality control, the tire will be palatized and coupled to the RFID tag which is applied on the pallet. From this point, the moment we created a “mother/child” relation between the tires (children) on the pallet and the pallet itself (mother). Now, we only need to follow the pallets (warehousing, order picking, loading the trucks) since we already know which tires (children) are inside.
Suppose at quality control, a tire is rejected (normally around 2%) for whatever reason, with one push of a button we can download, real-time every process step of this rejected tire. Data collected from the building area, molding, and quality control can be used to determine if a specific production line needs to be shut down and investigated. By using a simple RFID barcode bead label, it is very easy to diminish the number of rejected tires within the production processes. If, for example, the failure is caused by a defect segment in a mold. Again, with just one push of a button the tire producer is able to clarify which other tires have been produced by the mold. Locating those tires (mother/child relation between tires and pallets) within the warehouse or supply chain is a piece of cake, using RFID bead labels.
Automotive OEMs are requiring specific tires to be installed on each car during production. For safety, quality, performance and warranty purposes, OEMs are pushing tire producers to share more and more production and quality data for each individual tire. Using RFID tags and labels make this possible. The same RFID tags vulcanized in tires also enable a new generation of cars to register each individual installed tire in the ECU. Using an industry standardized ISO process, the tires RFID data is stored in the respective wheels’ TPMS sensor memory. This step can happen during the tire mounting process on the wheel or sometime before the wheel is mounted on a completed car. TPMS sensors are required on most vehicles for most global markets, and they are largely supported by most vehicles wireless ECU BUS. The vehicle simply retrieves the tire data from the TPMS memory and now has full awareness of the individual tires installed in each position.
Due to the variety of operating requirements and parameters that drive those, the production logistics of tires will change drastically. Today, large batches of the same tire are produced in large scale, while balancing productivity, efficiencies, quality, and manufacturing tolerances. Future production of tires for electric cars (but not just for electric cars) will require a different model, a model enabling much more flexible and diverse product offering of customized tires with specific parameters available within tight tolerances. Customers will require greater freedom of choice and tire offering suitable to their needs and environment. This requires a radical change in the production philosophy and processes of the tire industry, from manufacturing through logistics, service and installation. That radical change is the inclusion of RFID tagging devices with the manufacturing environment and end product.
About the Authors
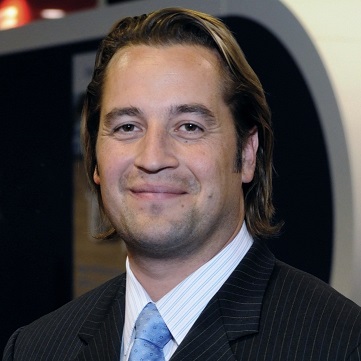
Jan Svoboda, Director, Business Development & RFID FineLine Technologies www.finelinetech.com Jan has over 20 years of experience in technology and solutions development within the high-tech industry. His extensive knowledge of RFID and wireless technologies is based on years in product development, product management, business development, sales and strategy roles at companies such as Zebra Technologies, SATO Corporation, SMARTRAC and Komtus.
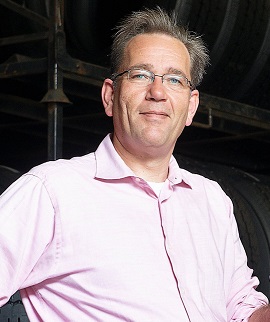
Jos Uijlenbroek was a co-founder of Ferm RFID Solutions, now a division of FineLine Technologies (USA). Jos has been instrumental in the design and implementation of RFID solutions for OTR, passenger, and TBR tires. He spearheads key international RFID-projects and partnerships. Jos is also a certified and pro-active GS1-member and guest lecturer at different Dutch universities.
Published in Telematics Wire