The Future of Automotive Industry is Electric and Autonomous
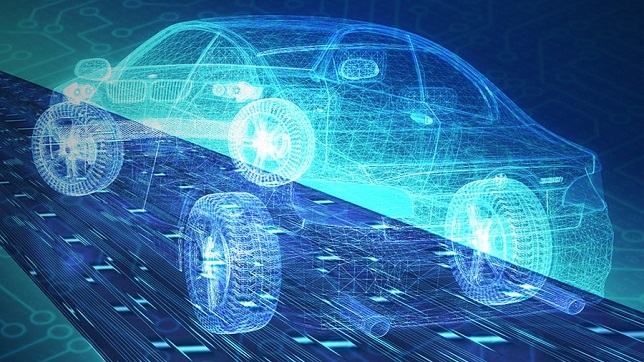
The socially conscientious customer today has made the switch from price-conscious purchasing to buying products that reflect their ideologies. From FMCG products, this trend is quickly making its way onto the personal vehicle market, as reflected by the rising popularity of electric vehicles. Government sanctions and the growing awareness of the effects of fossil fuel production and use has also driven car manufacturers to heavily invest in the research and development of electric vehicles. While innovation is accelerating the journey towards a cleaner and more sustainable future in the domain of mobility, the automotive industry is also rallying to meet the demanding deadlines and customer specifications for new vehicles.
Another important shift to be expected in road vehicles is the advent of autonomous vehicles. With several large warehouses across the globe investing in autonomous trucks etc., the age of autonomous road vehicles is not far away. The massive rate of electrification has also propelled carmakers to invest in R&D of autonomy since it is easier to implement autonomous features on electrified vehicles. As a result, electric vehicles are strongly accelerating the growth of autonomous vehicles.
Consumers are driven by technology and social awareness and demand both innovations within the same vehicle. Electric vehicles are built with drive-by-wire systems that replace traditional mechanical control systems with electronic controls. These enable the easy implementation of autonomous driving technologies. In addition, the fast-paced developments in battery technology, increase in range, increase in reliability of electric vehicles, will accelerate the speed at which autonomous vehicles can be developed.
Electrification – driving innovations in manufacturing
EVs are predicted to represent a third of the automotive market by 2025 and 51% by 2030.
Therefore, the automotive market landscape is evolving rapidly, with this change being driven not just by large household names but by new players. Some of these new players are content with low order volumes and using learnings to build their manufacturing workflows from the ground up; implementing newer smart technologies even in their manufacturing processes. This leaves conventional carmakers lagging behind newer companies that are more used to rapid innovation cycles and face low barriers because consumers expect more integrated digital technologies. Since new car designs render as many as 90% of automotive parts from existing ICE vehicles redundant, their strategies are less reliant on current supply chains and mass-manufacturing plants. The research finds that only 8% of carmakers see pure-play EV manufacturers as a threat, yet Tesla is already the market leader for battery electric vehicles (BEVs), while the likes of Lucid rapidly are scaling up with vertically-integrated EV production.
In contrast, data reveals a disconnect in the equivalent progress towards digital transformation by larger OEMs. While there has been a definite uptick in interest around “smart” automotive manufacturing, the research shows that recognition of its value is not always accompanied by implementation. Instead, the data reveals that the industry sees sourcing the required volume of parts and the inability to achieve economies of scale as the greatest perceived risk to the success of EV supply chains.
The challenges that automakers face aren’t always external. To make EVs more affordable at current order volumes while also delivering greater choice or ‘cars-to-order’, traditional high volume manufacturing lines need to transform more agile manufacturing infrastructure. They need to be built around speed to market. This can be challenging for incumbents, especially if they are still required to achieve the required profit margins.
Therefore, automotive OEMs must reconfigure traditional manufacturing business models to prioritise flexibility over process, empowering people with more integrated processes and greater automation.
To achieve this, there needs to be vertical integration of the development and manufacturing processes. At the same time, a deep focus on digital design and manufacturing approaches is key to agility. This transition isn’t easy since it necessitates a cultural shift within the organisation in addition to technology investments. OEMs are already making progress in this direction.
Overall, the data shows that there is growing interest in smart manufacturing approaches that apply pervasive connectivity, cloud and edge computing with momentum in data analytics, AI and robotics affirming that the industry is on the threshold of unprecedented change with very different ideas and levels of maturity on the journey to Industry 4.0. The convergence of these additional technologies will act as an adoption catalyst, with OEMs and their supply chains trying to adapt to this change as they evolve with the market.
Smart Manufacturing – Accelerating electrification
With the industry completely focused on the pivot to electric vehicles, manufacturing intelligence solutions like Hexagon are committing their resources, and innovations to build and optimize smart manufacturing solutions to accelerate the evolution and adoption of electric and autonomous mobility.
The low volume demand currently and an eagerness among venture capitalists to invest in electric mobility technologies has given smaller players a massive advantage in the current electric vehicle market. These smaller technology disruptors are taking advantage of the low entry barriers and also revolutionising manufacturing techniques with an agile development approach. To stay relevant in a rapidly changing market landscape like this one, the industry must adapt and reimagines processes and workflows that are currently used and taken for granted.
Hexagon recognises the opportunity that this offers to the automotive industry to drop the traditional volume-based approaches and completely revolutionize manufacturing by embracing intelligent solutions. Research from Wards Intelligence suggests that smart manufacturing, not scale, may be the key to success in the electric vehicle pivot. Hexagon’s smart manufacturing technologies provide several solutions for eMobility providers to optimise and validate battery designs using CAE simulation, ensure robust battery manufacturing processes with process simulation and execution tools, and verify components and battery systems through non-contact inspection and non-destructive testing techniques.
Examples on the ground
HV. Wooding, a key player in the renewable energy space has implemented Hexagon’s smart sheet metal cutting simulation software to optimize its production of components used in big-name car marques; supercar manufacturers; supercar e-racing; electric motorbike GP racing throughout Europe; railways; aerospace; and increasingly electric buses, construction and agricultural vehicles. In addition to drastically reducing their time to market for new customized components, the company also uses Hexagon’s RADAN to quote prices and timelines for manufacturing, thus bringing great certainty into their manufacturing projections.
The acquisition of Romax Technology has also enhanced Hexagon’s product suite in the electromechanical drivetrain design and simulation space. simulating the operation of the entire system – engine, gears, bearings and housings – the efficiency of automobile, aerospace and wind turbine powertrains can be optimised, and the battery range of electric vehicles can be increased. The acquisition of Romax Technology enables Hexagon to meet the growing need for electrification, by providing our customers with integrated tools to develop the next generation of energy-efficient electric vehicles.
Another disruptor, Helix Technologies, implemented antenna designs using electro ceramics, printed with toolpaths on a bespoke scientific laser lithography processing machine programmed by Hexagon’s ALPHACAM, to synchronise information from multiple networks through the GNSS (Global Navigation Satellite Systems).
The way ahead
At Hexagon, we’ve created the 100% EV initiative to accelerate the successful pivot to electrification in the automotive industry. Hexagon aims to offer a new set of smart manufacturing technologies for eMobility, blending our experience in automotive design and engineering, production and metrology to help you make the journey toward 100%EV faster and more cost-effective.
With our expertise and deep knowledge of best practices from automotive, electronics and other key industries, together we will make the production of electric vehicles easier, increasing your productivity, lowering your costs and reducing time to market. Hexagon aims to drive its holistic approach to benefit manufacturing experiences, as well as the environment, the result being a smarter, more sustainable world for us all.
Author:
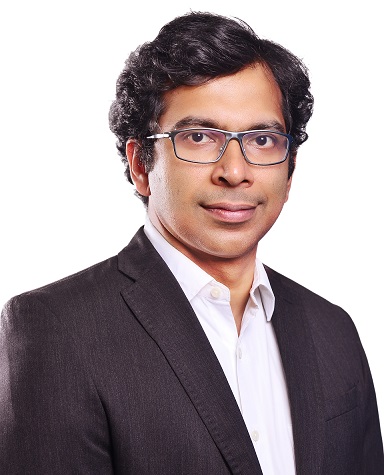
Bhavaneesh Athikary
Automotive Lead, Indo-Pacific
Hexagon
Bhavaneesh has over 16+ years of experience in Automotive domain, most of which is focused in the field on engineering simulations for automotive OEMs. Currently, he heads Automotive, Business Development for automotive industry in Indo-pacific region. As a part of this job, he works closely with all major automotive OEMs and suppliers in Indo-Pacific region, helping them solve their engineering challenges.
Published in Telematics Wire