Performance Simulation and Virtual Testing
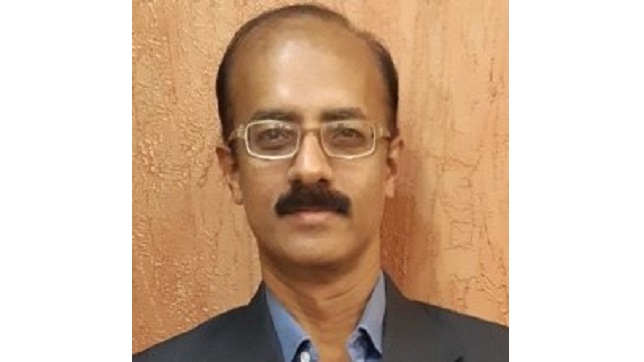
Automotive industry is currently experiencing major changes on multiple fronts. We are noticing more consolidation and growth of electric vehicle market, more focus on connected and smart vehicles and more interest on autonomous and advanced driver-assisted vehicles. Exploration of fuel cell technology is also happening simultaneously. Despite these very advanced developments, the traditional vehicle development process has retained its importance and even become more sacred now than ever. The automotive industry has very well realized that the huge investments involved in a vehicle development program will be at stake if a structured development process is not followed properly.
Vehicle development typically follows a V process which focuses equally on the digital product development and the test and validation of the new vehicle before launch. The left arm of the V indicates the cascaded development process – from component to subsystem to vehicle. At every stage of the development the intended performance is validated by physical testing depicted by the right arm of the V process. But we need to keep in mind the huge expenses and enormous preparations involved in physical tests and validation. Simulation tools have become very handy in reducing the number of tests required as they provide good confidence of the product’s performance during the digital development phase. During the last two decades, we have seen phenomenal advancements in simulation methodologies to virtually test the performance parameters like driving dynamics, cooling, safety and acoustics which have resulted in a drastic reduction of the number of vehicles planned for physical testing.
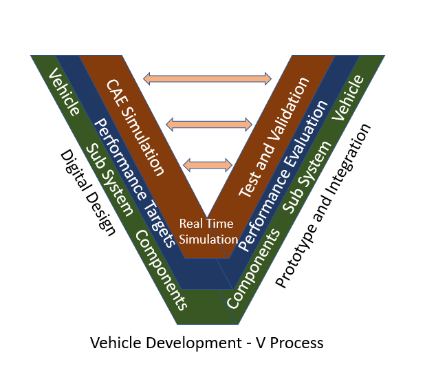
In spite of such advancements, it has been observed that there are still some gaps between physical testing and simulation-based verification as the traditional virtual simulations seldom take into account the real-time incidences. For example, a driver encountering an unexpected obstruction would try to drive away with a sharp steering maneuver. Performing a simulation for such encounters were not possible till recently but the product developers have started performing co-simulation and Software in Loop (SiL) simulations to understand real-time events.
In addition to the current breakthrough technology shifts in the automotive world, the emphasis given to safety aspects has also gone significantly high. The traditional simulation and test approaches focus more on the energy absorbing vehicle structure, safe seats, seatbelt restraints and airbags. These focus areas are referred as passive safety areas. Last few years, automotive industries have started focussing more on active safety measures including Electronic Stability Controls (ESC), Autonomous Emergency Braking (AEB) and Adaptive Cruise Control (ACC).
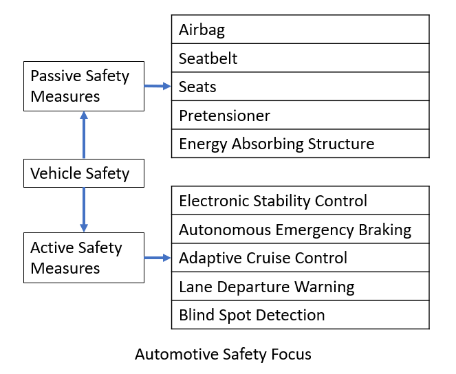
The real time simulations need to necessarily include the active safety measures to understand the vehicle behaviour during unexpected events. Software in Loop testing framework helps to understand the real time vehicle simulations with a good accuracy.
A recent study shows that more than 40 percent of fatal single vehicle accidents happen due to vehicle rollover. Most of the times, the rollover happens due to sudden attempt made by the driver to manoeuvre an obstacle on his way. Another reason for rollover is the misjudgement of curvatures. Electronic Stability Control plays a major role in preventing the ‘loss of control’ situations by applying brakes on the respective individual wheels to prevent the unintended heading direction leading to spinning. A co-simulation approach using an MBD Software like ADAMS and MATLAB will be able perform the real time simulation of vehicle manoeuvres. In fact, the Electronic Stability Control module can be developed by combining the vehicle Multibody Models and MATLAB Controls and the same can be calibrated with test results so that the same can be used for any complex drive simulations. Such simulations help the vehicle designers to develop the control algorithm for the vehicle stability.
VTD (Virtual Test Drive), a toolkit from MSC Software is used for the development of Physics based sensors (Radar, Lidar and Camera), ADAS and automated driving systems. It covers the full range from the generation of 3D content to the simulation of complex traffic scenarios and, finally, to the simulation of either simplified or physically driven sensors. It is used in Software in Loop and Hardware in Loop applications. Due to its open and modular design, it can easily be interfaced and integrated as co-simulations including 3rd party or custom packages.
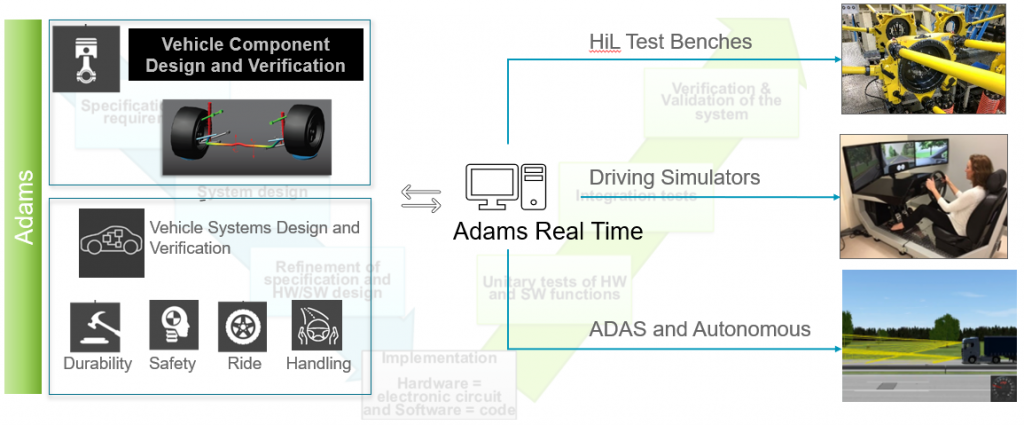
Another good example co-simulation from safety point of view is the performance prediction of ABS brakes during real time braking events. Multibody Simulation tools like ADAMS along with the ABS control modules developed using MATLAB-Simulink will be able to help the vehicle designers to predict the performances of the vehicle under various driving conditions and braking events. Such simulations also help to finetune the design and the control algorithms to meet the brake system performance targets.
An important area of vehicle safety is the protection of its occupants. Airbags along with seatbelt form the primary protective system for the occupants. The most crucial aspect of the airbag system in the event of a collision is its deployment timing as the entire collision event takes place in a few milliseconds. In addition to performing various crash simulations, tools like LS Dyna help the airbag sensing system development by providing the impact pulses, the basic input for the sensing system.
The enhanced capabilities available with structural simulation tools like ANSYS, OPTISTRUCT, ABAQUS and NASTRAN have great potential to be a part of co-simulation for structural optimization and vibration control by focussing on real time scenarios and help the vehicle industry to develop great products.
Author:
Dr. Manivasagam is the Global Head of Vehicle Engineering at Tata Technologies. His current focus areas include simulation driven design and development, vehicle tests and validation, vehicle integration and vehicle attribute management and balancing.
Dr. Manivasagam received PhD in 1994, for his research work on Damage Progression Studies in Composite Materials from Anna University, Chennai. He holds Master’s Degree in Engineering Design from Anna University and Bachelor’s Degree in Mechanical Engineering from University of Madras.
Published in Telematics Wire