Precision and Complexity: Role of Manufacturing in Product Performance
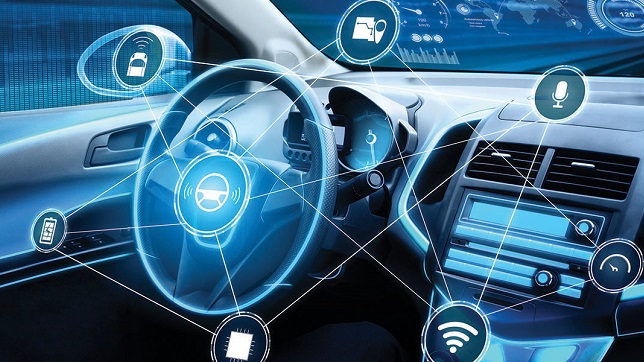
We generally talk about advance IoT solutions which should be very precise in performance with low latency rate and highly reliable, but supply chain has become the new agenda post COVID era. Today, the electronics industry faces significant challenges in terms of raw materials, component prices and logistics.
Let me just take one example here to begin the discussion around manufacturing and its challenges. With this change in requirements over a decade, we moved from basic telematics to advanced phase of telematics which is known as Advanced Driver Assistance System (ADAS). Advanced means more and more features, high performance, better accuracy which further means, more components on the boards and complex PCB design.
Any electronic hardware must pass through multiple phases of production. In this article we are specifically talking about the complex electronic device manufacturing phases.

Demand for advanced driver assistance systems (ADAS) is at an all-time high, and with it, the need for evolving manufacturing and sourcing protocols for the automotive industry. he market is further expected to grow at a CAGR of 16.85% in the forecast period of 2022-2027 to reach a value of approximately USD 68 billion by 2027.
Design of Hardware
Design of PCB is the crucial piece of puzzle. Seeing the current market trends, where electronics is completely imbalanced, choosing the right component for your design is very important. It takes the round of discussions with suppliers on both prices and lead time. Today’s trends show that demand for IoT products is growing rapidly and will continue to increase in the future. In early 2021, most factories announced the increased lead time, and now we hear more and more about delays in the supply chain.
Choosing the right manufacturing partner who has all the quality checks in place and having excellent SMT lines, plays a vital role in the performance of finished product. A typical ADAS device features a suite of sensors. As the complexity and capability of these sensors increase, so does the cost. Supply challenges affect the timeline of widespread adoption.
Test Standards Enables Smooth Performance of ADAS
It is a complex engineered product, demands top notch quality during production phase. To be precise, the PCB itself comes with minimum 10-12 layers to justify the design. Apart, the testing of assembled boards is another important procedure that has significant role to play. In-Circuit Test, ICT is a powerful tool for printed circuit board test. Designer is forced to bring out many test points, which is in direct conflict with his goals to miniaturize the design.
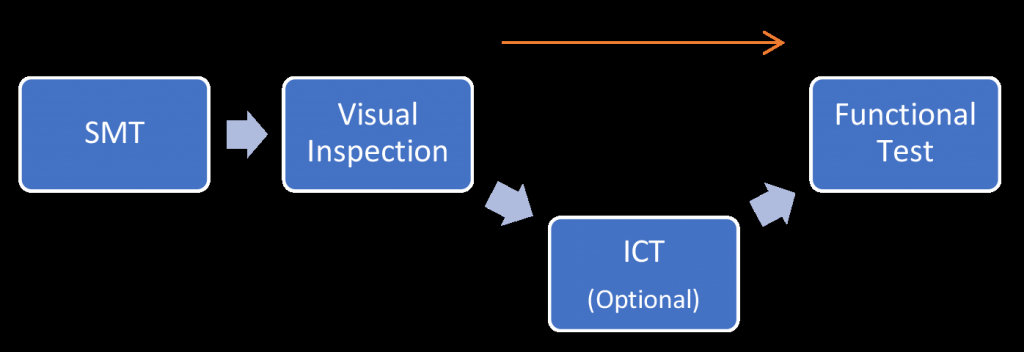
ICT equipment provides a useful and efficient form of PCB test by measuring each component in turn to check that it is in place and of the correct value. As most faults on a board arise out of the manufacturing process and usually consist of short circuits, open circuits or wrong components, this form of testing catches most of the problems on a board. These can easily be checked using simple measurements or resistance, capacitance, and sometimes inductance between two points on the circuit board.
Then, we come to Functional Test (FCT), is a PCBA functional test. It is done mainly to simulate the product working environment to verify the function of boards during working conditions. If any of these two tests are skipped during the manufacturing specially in case of automotive products, the entire credibility goes for a toss!!
The technological components harnessed in ADAS require precision engineering. They are complex, sensitive to environmental effects and thus require protection. For example, the mechanical housing of ADAS element must be resistant to the effects of corrosion, humidity, shock and vibration.
Right Manufacturing Partner Can Solve the Puzzle
We at Napino Auto and Electronics bring the expertise in high class manufacturing facility and all the ISO standards in place which are required for an automotive manufacturing setup such as IATF 16949, ISO 45001, ISO 18001.
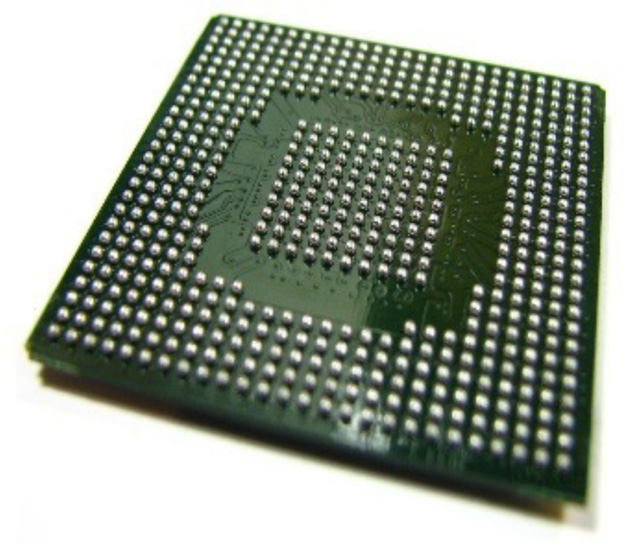
Having the dedicated test labs, certification facility, part to part traceability makes us up in the industry to be considered as the first choice as the preferred manufacturing partner.
Attributes of the perfect EMS provider:
- Components Storage, Verification and Traceability
- In line Solder Paste Inspection
- 3D Automatic Optical Inspection
- Continuous profile monitoring of reflow oven
- PCB Cleaning
- ESD (Electrostatic) Control workstation
- Clean room with class 100,000 or above
- Nitrogen and lead-free compatible soldering
- In line X-Ray Machine
When it comes to complex PCB boards, discussion over BGA (Ball Grid Array) components can’t be ignored. Reason being, these are the heart of the design and very costly. Taking the high level of precautions such as adequate solder paste, reflow are the standard practices to be followed. Any ignorance in the process can lead to huge loss of PCBs and hence the money. X-ray inspection is the right approach here to ensure the perfect soldering of module which can’t be seen through naked eye.
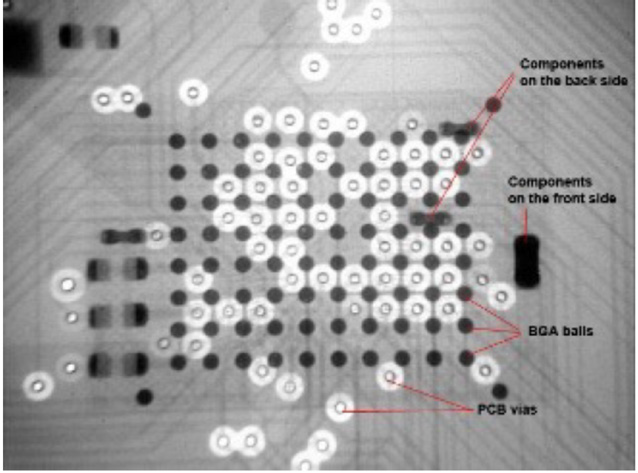
Process Failure Mode Effects Analysis (PFMEA) is a structured analytical tool used by an organization, business unit or cross-functional team to identify and evaluate the potential failures of a process. PFMEA helps to establish the impact of the failure and identify and prioritize the action items with the goal of alleviating risk.
Author:
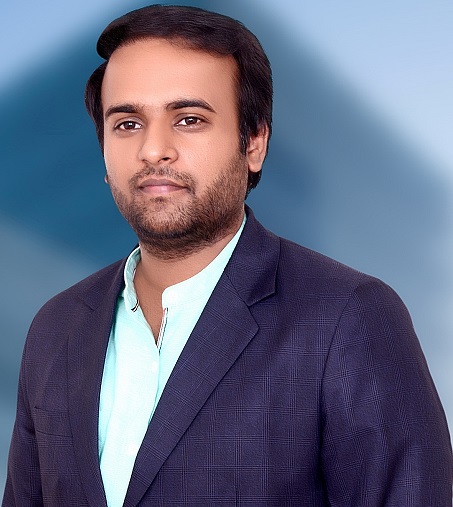
Aman Jain
National Sales Head-IoT, Marketing & BD
Napino Auto & Electronics Ltd
I am Aman Jain, having 9+ years of experience of Business Development in Vehicle Telematics Domain along with deep understanding of Industrial IoT and Electronics Manufacturing Services. I have spent most of my professional journey in Vehicle Telematics itself. My core strength has been to understand the potential opportunity in the market for IoT sensors, specifically in connected technology.
Published in Telematics Wire