Role of Automotive Ethernet in Offroad Vehicles
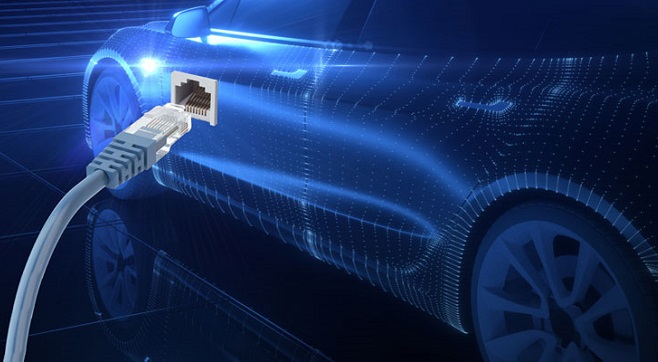
Offroad/ heavy-duty vehicle architectures are evolving day by day and getting smarter with increased use of various electrical and electronic components, thus increasing complexity and more and more software functionality running inside the vehicle. This modern vehicle architecture demands higher bandwidth with faster data throughput for In-Vehicle communication, an easily scalable network to adopt additions of new electrical and electronic components and more flexibility in integration with various services (cloud and consumer products). Automotive Ethernet offers super-fast speed and high bandwidth, which is a must for next-gen off-road vehicles like Agriculture and Construction equipment to support high performance vehicle functions.
Limitations with Other Automotive Networks
The current industry, the dominant technology for in-vehicle networking is CAN/CAN-FD/CAN-XL developed by Bosch has been a lifeline for all automotive companies. CAN Bus offers speeds up to 10 Mb/s (with CAN-XL) which is much less than what a new-age vehicle demands. CAN supports a limited fixed message size of 8 bytes with CAN, 64 bytes with CAN-FD and 2048 bytes with CAN-XL is not efficient for many applications as applications need variable data rates and different message sizes.
FlexRay is another in-vehicle network protocol which offers clock synchronization, built in redundancy and TDMA (Time Divided Media Access to avoid collisions) but only offers 10 Mb/s of bandwidth.
On the other hand, MOST bus offers synchronous communication with maximum bandwidth up to 150 mbps.
Figure 1 shows a comparison between automotive networks in terms of network scalability against bandwidth.
Why Automotive Ethernet?
Automotive Ethernet is a physical network used to connect different vehicle components which fully meets automotive standards and IEEE 802.3 specification. The automotive ethernet is a single twisted pair of copper cables which is designed to meet automotive electrical requirements and regulations in mind. The automotive ethernet exists in many forms and with many performance levels ranging from 10 Mb/s to beyond 5 Gb/s. Currently, the main variant in the market is 100BASE-T1, 1000BASE-T1 used by many OEMs. One of the main advantages apart from speed is no collision of messages due to its full duplex nature, all traffic is bidirectional, which makes the ethernet the fastest electrical solution. This super-speed network helps machine critical applications & time-sensitive applications that need close to real-time message delivery.
Different topologies of Ethernet support easy scalability of the network, which means to expand the network we add ethernet switches which help add more nodes to the network. An Ethernet switch is an intelligent device that has capabilities of message routing, priority, scheduling and so on. So, the ethernet switch enables us to extend the vehicle network as we want. Also, arbitration is done inside the switch itself, hence we don’t need to worry about link access arbitration.
Ethernet supports variable frame sizes ranging from 84 bytes (control messages) to large messages of 1500 bytes (camera streams and heavy payload transfer needs), which makes it ideal because different use-cases need different message sizes. The resulting latencies, considering 100BASE-T1 vary from 6.72µs for short messages to 122µs long messages and if we consider latencies for 1000BASET1 networks (which is a favorite amongst many OEMs) is much less and ideal for all high-performance applications.
Ethernet offers different communication schemes; unicast, multicast and broadcast. Applications can be used as per their needs, so Ethernet is flexible.
Ethernet has multilevel protocol alternatives to choose from as per needs while implementing communication in vehicles.
Applications of Ethernet in Off-road vehicles
Below are some use-cases of Ethernet in off-road/heavy-duty vehicles, but not limited to them, there are numerous applications we can think of using Automotive Ethernet.
Diagnostics and Reprogramming
Diagnostics over the ethernet is much faster than traditional diagnostics over CAN. Diagnostics over IP i.e., DoIP (ISO 13400-2) is a standardized protocol used as a transport layer for Unified Diagnostics Services (UDS ISO 14229-5) unlike over Diagnostics over CAN (UDS 15765-2).
As the number of high-performance ECUs/VPUs are included in off-road vehicle architecture nowadays, reprogramming of the controllers (offline or over the air) is getting challenging due to relatively large size of software payload compared to the smaller payload of traditional ECUs. The faster reprogramming is needed for an hour and that really depends on the payload transfer rate onto end controller. The ethernet helps with faster payload transfer, thus ensuring fast re-programming.
High Speed ISOBUS (HSI)
The Agricultural Industry Electronics Foundation (AEF) commissioned a 10th Project Team (PT10) to develop the next generation of ISOBUS to provide new capabilities well beyond CAN. High Speed ISOBUS (HSI) will pave the way for another major step into higher performance systems. The major backbone for the High Speed ISOBUS communications will be the automotive ethernet due to attributes such as communication speed, bandwidth requirements and control latency.
Machine control/Machine Automation
There are various use-cases where new-age machines need to collaborate with various sensors to capture data and, after applying intelligence, control the various parts/controls of the machine automatically while operating. As an example, in the agriculture industry, while planting the seed, planting at an accurate location with defined spacing between two seeds and within the farm boundary will need intelligent computation, taking various sensor data as input and controlling the nozzles of sprayer implement. This type of use-case needs super-fast communication throughout the vehicle network and the only way here is to use Ethernet backbone as networking.
Operator Assistance
Offroad vehicles are usually of large size and work in harsh environments where the operator doesn’t get a full view of the machine/operating area. Many vehicle manufacturers have many cameras installed in the vehicle for operator assistance; for example, precise maneuvering through the tightest space, machine control while performing work. These live camera streams are transferred to a PDU (primary display unit) in the operator station for operators to view and control machines (such as maneuvers, machine operation).
Functionalities like 360° surround views, bird eye view assist operator getting live streams to view the blind spots and make the decision. Using the automotive ethernet enables us to stream camera feeds onto display units (PDUs) without any extra wiring harness for cameras other than ethernet cable.
Remote Monitoring
New age farm management typically works like a farm manager managing operations to be carried on on the farm and keep assigning a job/work to an operator. In order to monitor real time, the machine needs to gather the work data continuously while the work is being done and stream data to the server. This kind of use-case requires high throughput in communication because the data needs to reach TCU (Telematics Control Unit) with close to no latency.
Perception-Based Solutions
Perception-based solutions are becoming popular in the off-road industry. Getting data from different sensors like GPS, cameras, engines and so on and running an algorithm to compute the next action for the vehicle to take and ask the machine to take the action is typically called perception-based actions. These types of solutions are not limited to a single use-case, there are various use-cases that can be drawn to make machines autonomous / semi-autonomous. The need for perception-based solutions is essential nowadays due to the degree of complexity in the new age vehicles and more and more components to control while running an operation. Control systems with Ethernet as connectivity capability or Ethernet as a major backbone, with CAN as internal communication to the control system is seen more efficient and profitable.
Machine to Machine Communications
In-field data sharing between machines is essential to share coverage maps between machines to ensure complete field coverage on display of a single machine (useful in low light or dusty conditions), eliminating application on already covered areas by another machine, monitor job done by another machine and sharing work history and shared work. These use-cases need wireless communication as the primary gateway and the ethernet as a backbone will improve the data latency in sharing data between vehicles.
Extended cloud Connectivity
Ethernet as a backbone network enables us to extend the internet reach to all ethernet capable ECUs/ VPUs/High-end computing devices from primary TCUs (Telematics Control Unit). This makes the controllers/devices independent of communicating with cloud services directly without the need to forward the data to middle-man.
Time sensitive Application
As we have seen so far in the document, we understand that there are multiple flows of data flowing on the Ethernet bus. Mostly there is no concept of “time” and cannot provide synchronization and precision timing. Delivering data reliably is more important than delivering within a specific time, so there are no constraints on delay or synchronization precision. Network congestion is handled by throttling and retransmitting dropped packets at the transport layer, but there are no means to prevent congestion at the link layer. The new standard Time-Sensitive networking is becoming popular for deterministic quality of services (QoS) for point-to-point communication by synchronizing time (synchronizing the clock of all devices contributing to communication), scheduling, traffic shaping and communication path (path selection, path reservation and fault-tolerance) are used for time critical applications.
Security in In-Vehicle Ethernet Networking
While addressing the demand for super-fast networks with high bandwidth, we also need to consider secure communication to prevent vehicles from cyber-attacks or protection against malicious attacks by humankind and considering aspects of confidentiality of data. As more and more use-cases of automatic machine control are becoming popular, protection against external attacks is very important. Attacks on the communication network can occur by deliberately inserting faulty messages or interfering with transmission messages (removing, delaying or modifying the message).
Generally, points of attack are external nodes such as OBD interfaces or wireless communication, but when the attack comes on the vehicle it can compromise the security of all networks. Hence, securing network communication is very important.
Securing networks starts with restricting network access by using authentication
The next level of security is securing on-board communication by using data authentication using symmetric cryptography and data encryption using secret keys.
Application-level security is applied using application-level knowledge to verify and restrict received data depending on the sequence of values or the condition of the vehicle.
It is assumed that malicious attacks change known communication patterns. Periodic messages are suddenly received in an irregular pattern or the MAC authentication for a message repeatedly fails. An extreme case is the denial-of-service attack in which messages are sent repeatedly with the goal of causing an overload. This significantly impairs normal communication. The detection algorithm can be implemented in application software on selected devices to detect anomalies. If such anomalies are detected, several modes of defense can be applied as required.
Things to watch
Adopting to the ethernet network has some costs involved, as for networking we need a switch as a separate hardware and the number of electrical or electronics components increases.
Multiple standards of ethernet communication need applications to make sure of compatibility between different versions of the standard.
Automotive Ethernet has a standard cable length of 15 meters; anything beyond 15 meters needs additional hardware repeaters.
References
- https://en.wikipedia.org/wiki/IEEE_802.3
- https://en.wikipedia.org/wiki/Time-Sensitive_Networking
- https://www.aef-online.org/about-us/activities/high-speed-isobus.html
- https://www.elektrobit.com/trends/automotive-ethernet-automated-driving-multi-level-security/
Author:
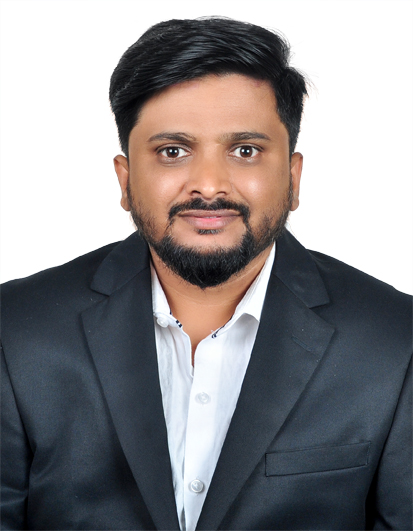
Swapnil Suresh Trambake
Solution Architect – Connectivity
John Deere India Pvt Ltd.
He is a software professional with 13+ years of experience in embedded software product development. He has been working with John Deere since 2016, starting as Lead Engineer and currently serving as Solution Architect for overall vehicle network connectivity with Ethernet communication. He has worked as a software architect for various embedded controllers, majorly Telematics Controller, Display Unit, Gigabit Ethernet Switch etc.
Published in Telematics Wire